Precipitates in creep resistant austenitic stainless steels
T.Sourmail
Department of Materials Science and Metallurgy
Pembroke Street, CB2 3QZ Cambridge, U.K.
Austenitic stainless steels are, by far, the most widely used stainless steels
comprising 70-80% of stainless production [1].
With excellent corrosion and mechanical properties at high temperatures,
they are choice materials for powerplant tubes which have to operate at
temperatures above 950K, or for aeroengines.
The important role of precipitation in the achievement of good creep properties
has been understood for long and extensively studied. Although some phases are
now well documented, there are still contradictions and missing
thermodynamic data, in particular, there is only a limited amount of
informations about phases like Z-phase or
Cr3Ni2SiN which can be predominant
precipitates in nitrogen bearing steels.
This paper is a review of common precipitates in austenitic stainless
steels, in particular wrought heat-resistant steels of the AISI 300 families or
20/25 steels. Precipitates forming in age-hardening austenitic stainless steels
are only briefly presented, having been previously reviewed by other authors.
Austenitic stainless steels are essentially
alloys of Fe-Cr-Ni, which owe their name to
their room temperature austenitic structure. The addition of chromium
has long been known to improve corrosion resistance. Cr is also a `ferrite
stabiliser' and Fe-Cr stainless steels have a ferritic structure, possibly
martensitic depending on the heat-treatment. The addition of austenite
stabilising elements in sufficient quantities can allow an austenitic
structure to be stable at all temperatures.
Nickel is the basic substitutional element used for austenite
stabilisation.
The equilibrium phases depend on the proportion of the three elements, as
well illustrated in an isothermal section of the ternary diagram for Fe-Cr-Ni
(fig. 1) calculated with MT-DATA [2].
Figure:
Isothermal section of the Fe-Cr-Ni diagram at
750
C: a typical 18Cr-12Ni wt% lies in the austenitic field.
Calculated using MT-DATA and the SGTE database.
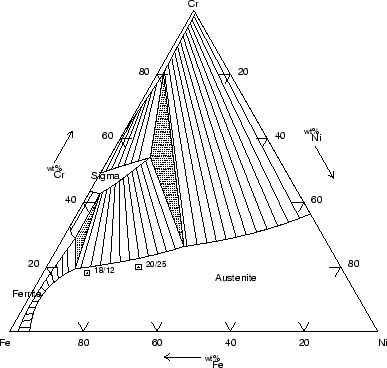 |
Often, alloying elements, either interstitial such as C or N,
or substitutional such as Mo, Mn, Ti, Nb, V, W, Cu, Al,... are used to
obtain the required properties.
They can be classified as ferrite-stabilisers or austenite-stabilisers and
their effect in this respect is often approximated using the notion
of chromium and nickel equivalents, calculated by formulae like
[3]:
In this example, the composition has to be given in weight%.
The use of such formulae is not always straightforward, as they refer to
the austenite
content, which is modified by various precipitation reactions involving these
elements.
Whether the austenitic structure is retained at room temperature
depends on the MS (martensite-start) temperature. Several empirical
formulae have been derived to describe the effect of chemical composition
on MS, an example is
[1]:
A typical type 304 (austenitic stainless steel) has its MS well below
room temperature.
However,
one should keep in mind that deformation-induced martensite formation can
occur well above MS. Md30 is the temperature at which 50%
of martensite has formed for a true strain of 30%. Again, formulae like:
have been derived to describe the effect of alloying elements
[1].
At high temperatures, a steel containing 18Cr, 12Ni wt% should
be fully austenitic. However, the addition of alloying elements often results
in the
formation of carbides, nitrides and intermetallics. These phases are not
always desirable and a good knowledge of precipitation reactions is required
to avoid loss of mechanical or chemical properties. A good example is the
sensitisation of non stabilised austenitic stainless steels: sensitisation
occurs when the precipitate
M23C6 forms at grain boundaries, depleting the
chromium content in the vicinity, which eventually results
in intergranular corrosion. This can be avoided by tying up the carbon with
strong carbide formers like Ti. The steel is then called stabilised.
These second phases will be presented in detail in a next section.
From a simple type 304 to the recent NF709, austenitic stainless steel
composition
covers a large range. The two main alloying elements are
chromium and nickel, so the steels will often be referred to
by their content of Cr and Ni. For example, 18/10 refers to an austenitic stainless steels with
18Cr, 10Ni wt% .
Table:
Composition of two austenitic stainless steels
Wt% |
C |
Mn |
P |
Ni |
Cr |
|
Type 304 [4] |
0.07 |
2.00 |
0.04 |
8-10 |
17-19 |
|
NF-709 [5] |
0.06 |
1.00 |
0.006 |
25 |
20 |
|
Wt% |
Mo |
Nb |
Ti |
B |
N |
Si |
Type 304 |
0 |
0 |
0 |
0 |
0 |
0 |
NF-709 |
1.5 |
0.26 |
0.05 |
0.005 |
0.167 |
0.40 |
|
The AISI 300 specifications for the compositions of different
austenitic stainless steels (wt%) is shown in table 2 (after [4]).
Grades denoted L contain low carbon (0.03 wt%) and N contain nitrogen
(eg: 316LN).
Most often used as creep-resistant steels are types 316, 321 and 347, or
alloys containing all of Mo, Nb and Ti.
There are many other variants of these compositions, like the japanese SUS300
series which mirrors the AISI 300 series, but with sometimes addition of both
Ti and Nb. For convenience, as is sometimes done in the literature, the AISI 300
series will be used even for steels not strictly belonging to it, like a 316 with
Ti addition.
In fact, it is not the intention to describe, in this review, the precipitation
sequences in all different grades of creep resistant austenitic stainless
steels, but rather to examine the occurrence of the various precipitates in
such a way that precipitation behaviour of non documented grades could be
inferred from the conclusions reached.
There is a large amount of material on the precipitation phenomena in the 300
series of alloys, which have been used widely as creep resistant steels.
The same is true for 20Cr-25Ni steels. However, it appears that the
long-term behaviour of Ti, Al alloyed austenitic stainless steels (type A286)
is very little documented [6]. This is possibly because
production difficulties have restricted the application of such steels to parts
requiring relatively small ingot sizes (aeroengine turbine discs), the design life
of which is much shorter than the few 100000 h required for a steam plant
[7].
- Mn has been introduced in austenitic stainless steels as a substitute for Ni during shortages
in the international market or for economical reasons. The nickel content can
be halved to 4 wt% by the addition of 2-6Mn wt%. However, although
the austenitic
structure is achieved, such steels do not exhibit the same corrosion resistance
as an 18/8 steel. Mn is also used to increase the solubility of nitrogen in
austenite.
- Mo is on the contrary a ferrite stabiliser. It improves the creep
properties of stainless steels by solid solution hardening. It also facilitates
carbides precipitation. However, it promotes
and Laves phase
formation on long term ageing.
- Stabilising elements like niobium, titanium and vanadium greatly improve
the creep strength of austenitic stainless steels mainly by precipitating fine carbides
intragranularly. On the other hand, they reduce the creep ductility. The ratio
in which they are added to carbon is important to maximise the strengthening
effect and avoid precipitation of detrimental phases.
They can also have a solid solution strengthening effect.
- Carbon acts principally by solid solution strengthening in non-stabilised
grades, but mainly by precipitation strengthening when Nb, Ti or V are present.
- Nitrogen is a strong austenite stabiliser. It has also a role in
increasing the creep life of austenitic stainless steels:
it can act like carbon in stabilised stainless steel by
precipitating in the form of titanium or niobium nitrides, but the
nitrogen remaining in solid solution has also a much greater strengthening
effect than carbon. It has been believed to also lower the diffusivity of
chromium and carbon in the matrix, therefore delaying coalescence of
precipitates [1],[4]. However, more recent results
indicate that nitrogen enhances chromium diffusion, but retards the nucleation
of
M23C6 because of its low solubility in this carbide [8].
The formation of MX precipitates in austenitic stainless steels occurs when strong carbides/nitrides
formers (Ti, Nb, V, Zr, Ta...) are added to the alloy.
These additions have two purposes:
- stabilising the alloy against intergranular corrosion. When stabilisation
is the first aim, a stabilising heat-treatment is conducted at 840-900
C
for several hours before service. Most of the carbon is then `tied-up' by
precipitation of MC.
- providing good creep resistance: when this is the first aim, a
solution heat-treatment is given in order to dissolve as much MX as possible.
Subsequent precipitation occurs during creep and increases strength. A typical
solution treatment is 30-60 min at temperatures between 1100 and 1250
C.
The second use is the one we will focus on.
Many studies have concentrated on MX precipitation, but also on the
appropriate content necessary to obtain the best properties. The solubility
of the MX precipitates and the stoichiometry are essential in determining the
behaviour of the steel with regard to precipitation.
MX carbonitrides have a NaCl fcc (face-centered cubic)
structure, with lattice parameters as listed in table 3.
Table:
Lattice parameter of some MX precipitates.
MX |
a, Å |
ref |
NbN |
4.39 |
JCPDS 38-1155 |
NbC |
4.47 |
JCPDS 38-1364 |
TiN |
4.24 |
JCPDS 38-1420 |
TiC |
4.33 |
JCPDS 32-1383 |
|
Often, measured lattice parameters have intermediate values,
reflecting the
existence of a solid solution between the different carbonitrides.
MX precipitates usually form on dislocations within the matrix, on
stacking-faults (most often with TiC), on twin and grain
boundaries. They have a characteristic cuboidal shape after sufficient ageing.
Stabilisers such as Ti or Nb have long been known to reduce the solubility
of carbon in austenite. Early studies of the problem consisted in the
determination of two parameters: H, the heat of solution, and A, a constant as
in:
where [M] is the weight percent of stabilising element in solution in
the matrix, and similarly for [C]. The product [M][X] is often referred to as
the solubility product. Strictly speaking, H is expressed in
K-1.
The two following relationships can be found in many publications
(e.g. [3],[4]):
They are essentially valid for a typical 18/12 steel, the concentrations
are in weight percent.
For a 20/25 steel, Kikuchi et al. [9] used for TiC H=10475, A=3.42
and for NbC, H=7900 and A=4.92, but it is not clear whether these values have
been measured for 20/25.
The solubility is, as shown in their work, an important factor in the
achievement
of good creep properties: they showed that adding M and X in excess of their
solubility limits resulted in coarse MX in the matrix and
induced faster coarsening of MX later precipitated. However, until this limit
is reached, the more M and X added the better because more MX particles will
be formed.
It is therefore clear that knowing the solubility limits of
MX carbides is
important. However, modern high-temperature austenitic stainless steels often contain both carbon
and nitrogen, and more than one strong carbide former (Ti+Nb, Nb+V...), and
relationships as above are of limited use when it comes to estimate
the solubility of multicomponent carbonitrides (e.g. (Ti,Nb)(C,N)).
Recently, some studies proposed
different approaches to the problem of the solubility of multicomponent
carbonitrides in austenite (P.Rios [10], [11], Zou et al.
[12]...). For example, Rios [10] proposed for Nb(C,N):
However, one must notice that all these studies deal with MX in austenite for
micro-alloyed steels. It seems clear, from the literature, that the presence
of Ni and Cr introduces a further difficulty in austenitic stainless steels, the main one being the
formation of Z-Phase.
There is a general agreement that Z-Phase (CrNbN) forms in Nb
stabilised austenitic stainless steels, with a sufficient amount of nitrogen.
In fact, it seems that as soon as 0.06N wt% is present in a
typical 347 steel, Z-Phase can be expected (Hughes, [13]).
Moreover, in Cr/Ni steels, MX precipitates have been reported
to start growing largely under-stoichiometric (Andrén et al. [14],
[15]).
No approaches have been found that dealt with the solubility of multicomponent
carbonitrides in austenitic stainless steels susceptible of Z-Phase formation. Indeed, Z-Phase is
even absent from the SGTE (Scientific Group Thermodata Europe)
thermodynamic databases accessed by programs such as MT-DATA or Thermocalc.
A number of studies have been devoted to the determination of the correct
quantities of M and X to use in order to have the best mechanical
properties. As stated above, one factor is the solubility of MX. This has
been clearly outlined by the work of Kikuchi et al. [9].
The second factor is the proportion of each element that has
to be added, in
such a way as to maximise the amount of precipitation for a given product
[M][X]. It is also important to know, if stoichiometry is not respected,
which of the elements is in excess, as this may influence the precipitation
sequence.
Wadsworth et al. [16] proposed a quantitative approach to stoichiometry and showed that the amount of precipitate that can form
drops quite sharply when M and X are not added in proportions corresponding
to the composition of the expected carbide (figure 2). Using the data of Keown and Pickering [17], they showed that best creep lives were
obtained when the Nb/C ratio was matching the stoichiometry
Nb4
C3 (for 18/12 or 18/10).
Figure:
The amount of niobium carbide available for
precipitation at 923K (after solution treatment at 1373K) as function of
the degree of deviation from stoichiometry r, defined by
r=pBT-qAT, where p and q are the mass fractions of A and B in the
compound ABn, and AT and BT the mass fraction of these elements in
the alloy. After [16]
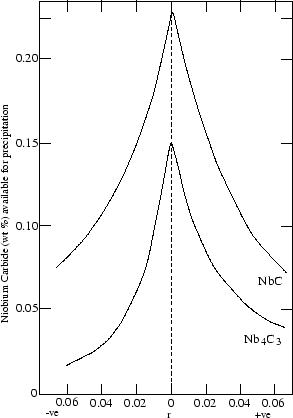 |
Other studies have shown that best creep life was obtained for a
Nb/C atomic ratio of 1/1 (Adamson and Martin [18], Kikuchi et al.
[9], all for 20/25).
The work done by Kikuchi et al. does not highlight any serious contradiction
since the first composition they tried around the atomic ratio
1:1 was 2:1, which means that any variation within this interval was not
investigated. However, Adamson and Martin have results for the weight ratios
8:1 and 10:1 (respectively atomic ratios 1:1 and 4:3), but find better creep
properties for the 1:1 atomic ratio. A possible explanation is that NbC
actually forms with the stoichiometry 1:1 in 20/25 steels.
It seems important to note that all these studies rely on relatively
short term creep tests (as an average, less than 1000 h). No study has been
found which confirms the importance of stoichiometric addition in long term
creep properties. Moreover, this explanation of the good creep properties of
steels with stoichiometric additions of M and X assumes that MX precipitates
form with their final stoichiometry, which has been proved wrong by different
authors.
The non-stoichiometry of MX precipitates in 18/12 austenitic stainless steels has been confirmed
by microprobe analysis (Andrén et al., [14], [15]).
The authors noticed that MX was largely sub-stoichiometric for short ageing
(typically 3 h at 750
C), and contained a large amount of Cr
substituting for
M (Ti,Nb,V...). They proposed the following explanations:
as MX has a lattice parameter larger than that of the austenite,
a flow of vacancies is needed for the growth of MX and stress is generated.
The substitution of M by Cr and the low carbon content both reduce
the lattice parameter.
Moreover, Cr is readily available while M has to diffuse over long distances.
The formation of sub-stoichiometric, carbon depleted MX precipitates is
therefore kinetically advantageous.
In more theoretical terms, this corresponds to two effects.
Capillarity is likely to
modify substantially the local equilibrium as the precipitates are very small.
In fact, the composition changes reported by these authors correlate
with size changes.
The second effect is the modification of local equilibrium to satisfy
simultaneously the flux balance for different solutes.
This effect could affect strongly the composition of MX, since the
diffusivities of the elements involved are very different. It
would similarly correlate with a size change unless the precipitates are only
coarsening.
However, stoichiometric carbides still have a lower free energy
and, during further ageing, they grow at the expense of sub-stoichiometric
ones. This is because, according to Andrén et al., the diffusivity of
metallic elements within MX precipitates is so small that these precipitates
can not change composition [14].
Z-Phase is a complex carbonitride which forms in Nb stabilised austenitic stainless steels
containing a relatively high level of nitrogen. It has only recently been
discovered, with its structure being fully determined by Jack and Jack in
1972 [19], and it appears from the most recent reviews (e.g.
[3]) that the conditions of its formation are not very clear,
and even less is its relative stability when compared to other carbonitrides.
The structure of Z-Phase is commonly accepted to be the one described by
Jack and Jack [19]: it has a tetragonal unit cell (space group
P4/nmm), with
a=3.037 Å and c=7.391 Å. The unit cell is obtained by ordering of Cr, Nb
and N atoms, the formula being
Cr2Nb2
N2 per unit cell.
Vodárek [20] reports the following orientation relationship for
Z-phase in a type 316LN:
In contrast to MX precipitates, it seems that Z-Phase dissolves little (if
at all) substitutional elements. Raghavan et al. [21] suggest that
it can dissolve carbon and write CrNb(CN), without giving any
evidence for this. The absence of a CrNbC phase suggests that if carbon can
dissolve in
Z-Phase, it can only do so within limits. Also, when Nb is in sufficient
quantity, both Z phase and NbC are found.
Z-Phase is seldom reported, even in alloys liable to form it on ageing.
This could be due to its composition and its general features of formation
which are not very different from common MX precipitates.
It generally forms on grain-boundaries, very rapidly, but also on
twin boundaries and within the matrix, where it is associated with
dislocations [22]. When it forms, it is usually as a fine dispersion
of particles (see [13],[21], [22]), which makes
it an interesting phase when good creep properties are sought.
The morphology has been reported to be either cuboidal
[22] or rod-like [14].
There is a good agreement that it forms at high temperature:
Raghavan et al. [21]
report its formation during annealing (1 h at 1300 K) of a
18/12 containing 0.3Nb wt% and 0.09N wt%, with an orientation relationship
indicating that these are not residual particles. After ageing 8000 h
at 866 K, it is still the predominant precipitate.
Few
M23C6 and
-phase particles are present.
These authors indicate that a 10 s heat-treatment at 1573 K is sufficient to
dissolve all the Z-phase particles, which is not inconsistent with the work
of Robinson et al. (quoted in [21]) which locates the solvus of
Z-phase to be between 1573K and 1623K in a steel containing larger amounts of
niobium and nitrogen.
Robinson and Jack [22] report the formation
of Z-Phase in a 20Cr/9Ni
steel containing 0.38N wt% and 0.27Nb wt% between 700 and 1000
C.
At 1000
C Z-Phase is the first and only phase formed. It is found
uniformly distributed after 30 min but coarsens rapidly.
At 700
C it starts to precipitate in the matrix after 16 h.
At lower temperatures, Vodárek et al. [23] report a considerable
dimensional stability of Z-phase in a type 316LN, with a mean size
of 6nm after 82 h at 650
C and 12nm after 37890 h at the same
temperature.
Thorvaldsson and Dunlop [24], studying the effects
of stabilising
elements in austenitic stainless steels, use a 18/12 steel with 0.4V, 0.13Nb and 0.43N at%.
After 5000 h at 750
C, no Z-Phase has formed, but a (Nb,V)(C,N)
fcc carbonitride forms instead.
Andrén et al. [14], with the same composition,
in very similar conditions, found, on the contrary, that the MX
precipitate had always a stoichiometry not far from M
X0.5, and
contained sensibly as much chromium as Nb+V. However, the characteristic
tetragonality was not observed and the authors suggested that they found a
precursor state of the fully ordered Z-Phase.
It seems quite reasonable to propose that Z-Phase is the stable Nb containing
phase in austenitic stainless steels with high nitrogen: Hughes [13] suggests that it
can be expected in a typical 347 steel as soon as the weight percentage of N
is greater than 0.06 wt%. Knowles [25] find Z-phase in a
20/25 0.41Nb wt% steel with 0.028N wt%, which could indicate that chromium
and/or nickel content play an important role in the solubility of this phase.
The problem arises, in many steels, to know whether NbC or Z-Phase is the more
stable. Very few studies have dealt with additions of Nb, C and N
together in a way that could determine which phase is more stable: often
Nb is in excess and both NbC and CrNbN form. Uno et al. [26]
found that only Z-phase formed in a 18/12
Nb steel with carbon and nitrogen, the niobium content being lower than that
required to combine either all C or all N. This would indicate that Z-phase
is fast enough to form first when competition between NbC and CrNbN is
likely to occur. On the other hand, Knowles [25]
reported Nb(C,N) after 2 h at
850
C in a 20/25 steel, transforming to Z-phase with further ageing.
From the precipitation behaviour of NF709 [5], where
Z is reported after ageing times of 104 h at 750
C,
and C containing phases are
M23C6 and
M6C one can
infer that Z-Phase is more stable than NbC and that the latter will dissolve
for the former if Nb is in too small quantities.
However, Raghavan et al. [21] deduce from a comparison between 347
(18/12 with 0.8Nb and 0.07C wt%) and 347AP
(18/12 with 0.3Nb, 0.09N, 0.009C wt%)
a greater stability of NbC, since Z is found to precipitate from the solid
state but the NbC is found as residual particles. The conclusions of such a
comparison have to be examined carefully as the compositions were different.
Generally, one can conclude that Z-phase precipitation is not fully understood.
Points of agreement are its stability at high temperature and the features of
its precipitation (fine dispersion), proposed solvus temperatures are different
between the studies, but these differences are consistent with different
compositions.
It is difficult as yet to build a coherent view of the different kinetics
observed. It is not clear whether Z-phase actually forms from MX precipitates
as suggested by the results of Knowles [25] and Andrén
et al. [14], or directly as suggested by Robinson et al.
[22].
These observations could be reconciled if one could prove that the driving
force in a 20Cr 10Ni (Robinson et al.) is significantly different than that of
a 18/12.
The importance of Z-phase in both ferritic and austenitic power
plant steels, renders particularly necessary the assessment of the ternary
system Cr,Nb,N to provide the thermodynamic parameters required for any
prediction.
M23C6 is a more general notation for
Cr23C6, as often,
Ni, Mo and Fe are found to substitute partially for chromium. It is the main
carbide in non-stabilised C containing austenitic stainless steels; nitrogen bearing steels form
Cr2N.
It has a fcc structure (and space group Fm3m) of
lattice parameter varying between
10.57 and 10.68 Å, which is about three times that of the austenite. It is
often reported to grow with a cube to cube orientation relationship:
It is most of the time the main carbide found in austenitic stainless steels.
Although it can be only metastable, it is always found in the early stage of
precipitation because it nucleates very easily.
M23C6 is most of the time reported to precipitate on the following nucleation
sites, and in this order: grain boundaries, incoherent and coherent
grain boundaries,
intragranular sites. In Nb stabilised grades, it is sometimes reported
to nucleate on undissolved (that is, during the solution treatment)
niobium carbonitrides.
Generally,
M23C6 only shows
and
interface planes. This has been explained by Beckitt and Clarck
(1967, [27]), who showed these planes have the best atomic
correspondence with the austenite.
The precipitation of
M23C6 has been the focus of many investigations,
motivated by its importance in terms of corrosion resistance.
M23C6 on grain
boundaries is often associated with intergranular corrosion. It is found after
very short ageing times (30 mn at 750
C,Lewis et al.,[28]), even
in stabilised steels. It causes the grain boundary to move, and therefore
shows on one side, the new grain boundary, while the other has a serrated
aspect composed by the
interfaces. These precipitates
are usually large. When boron is added, the number density of
M23C6 along the
grain boundaries increases (Tanaka et al.,1997, [29]), with beneficial
effect for the creep rupture strength, as the grain boundary sliding and
surface cracking are reduced.
Other effects of boron in
M23C6 will be dealt with later.
Figure:
M23C6 on grain boundary.
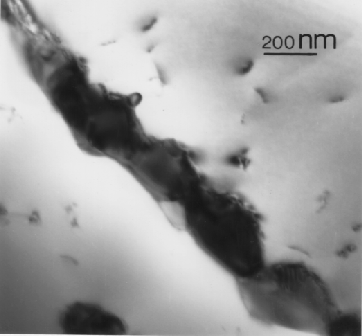 |
On incoherent and coherent twin boundaries,
M23C6 forms long plates parallel
to the twin boundaries. The plates are, as for any form of
M23C6 in austenitic stainless steels,
bounded by
and
planes only.
The large faces are
planes parallel to the twin
boundaries. Plates are initially growing from the incoherent twin boundary,
but some are found later apparently detached from the boundary. Precipitation
on the coherent boundary occurs more slowly than on incoherent ones.
Figure:
Plates of
M23C6 growing from an incoherent twin
boundary (left), and around a Nb(C,N) precipitate (right), work done for
this project.
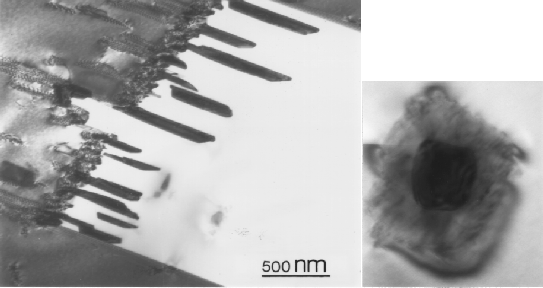 |
The mechanism of their formation has been subject to
controversy: Beckitt and Clarck (1967, [27]) suggested that
carbides growing on the incoherent twin boundary repels Shockley partial
dislocations in the twin, and these cause nucleation of new plates
in the twin. But detailed observations have lead Singhal and Martin (1967,
[30]) to conclude that stacking fault were first growing in the twin.
M23C6 would then nucleate on the Shockley bounding dislocation and grow
in the stacking fault, possibly helped by an enrichment of this stacking
fault in chromium.
Both fail to explain why these plates most of the time stand
separated from the boundary and from each other (according to these mechanisms,
they should be connected to the incoherent twin boundary by a stacking fault).
Another mechanism has been proposed more recently by Sasmal (1984,
[31]). Noticing that plates do not form away from the boundary or
on coherent twin boundaries if the samples are
directly put at ageing temperature after the solution treatment, Sasmal
suggested that the formation of plates of
M23C6 close but detached from
the incoherent twin boundaries, and on coherent ones, was an effect of
residual stress developed in these regions. One could here argue that stress
only influences the formation: if it favors the formation of
M23C6 plates
parallel to the twin boundaries, there should still be a small percentage of
plates growing in other equivalent directions.
In the austenite grains,
M23C6 precipitates as cuboids or plates. The latter
have the same characteristics as the plates growing from twin boundaries. The
cuboids grow on dislocations until they form a continuous chain sharing
their corner. These chains can form branches, forming secondary stringers of
M23C6.
Beckitt and Clarck (1967, [27])
have proposed satisfactory explanation for the formation of
these secondary stringers: the growth of primary
M23C6 generates dislocations
on which other precipitation can occur. The direction of these secondary
stringers is that expected by the mechanism, that is the direction of usual
edge dislocations in austenite.
Another kind of intragranular precipitation has been reported by Sasmal
(1997, [32]
). Plates of
M23C6 can form around undissolved Nb carbonitrides in Nb
stabilised steels. In this case, the large faces are
and
the edges are
. The reasons for this change are not clear,
although a contribution of the strain around the undissolved particle is
invoked.
M23C6 is, initially, a chromium-iron carbide. However, its
composition is susceptible to large variations. For example, in a typical
2.25Cr1Mo wt% steel,
M23C6 has a composition of about 0.3Fe, 0.38Cr, 0.1Mo,
0.22C mole fraction. While in a typical 304, it is closer to
0.04Fe, 0.65Cr, 0.11Mo, 0.22C.
There are also evidences that, for a given steel composition,
M23C6
composition
undergoes large changes in the early stages of the precipitates.
Lewis and Hattersley [28] quote a study by Philibert et al.
in which the authors propose that
M7C3 forms in the early stages of ageing
in a 18/8 steel, as the Fe/Cr ratio is more consistent with the known
composition of this phase. Similarly, Marshall [1] quotes a study
in which the authors show that up to 40 wt% Fe can be found in
M23C6 in the
early stages of precipitation, but also that the Mo content increases with
time.
It is proposed here that these composition changes can be explained by the
growth mechanism involved. In a multicomponent alloy, the interface has to
move at a rate which is consistent with the flux of each element, in order to
maintain local equilibrium. Therefore, the interfacial compositions are not in
general given by a tie-line passing through the bulk composition, but by an
alternative tie-line which permits the flux-balance (details are out of the
scope of this review, see for example [33] or [34]).
In the same way, on the interstitial lattice, B can
substitute for C; however both in very small quantities.
Boron is of particular interest as it promotes the formation of
intragranular
M23(C,B)6.
There is some controversy about the mechanism involved, but it is possible
that B increases the lattice parameter of
M23C6, therefore reducing the
mismatch with the austenite. The presence of B in
M23C6
has been shown using Atom
Probe Field Ion Microscopy (APFIM, e.g. [35]).
The same is not true for nitrogen. It has long been believed to have a small
solubility in
M23C6 (e.g. [36]). However, recent experimental results
supported by ab initio calculations indicate zero solubility of
nitrogen in
M23C6, the structure of which is destabilised if a small amount of carbon is replaced by nitrogen [8].
Except in the fine intragranular form,
M23C6 precipitation is not
desirable for good creep properties.
It is often associated with intergranular corrosion, as its
formation along the grain boundaries causes a local depletion in chromium and
possibly local loss of
the stainless property (the steel is then said to be sensitised,
i.e. susceptible of intergranular corrosion).
The solubility of carbon in austenite, with regard to
M23C6, has been described
by empirical relationships such as [37]:
Figure:
Solubility of C in austenite with regard to
M23C6
precipitation. Calculated with MT-DATA (allowing for austenite,
M23C6,
M7C3
and liquid, with elements Fe, Cr, Ni, 0.3Si, 1.0Mn wt%).
Solid lines for 18/12 and dashed lines for 20/25. The squares
correspond to the empirical relationship from
[37]
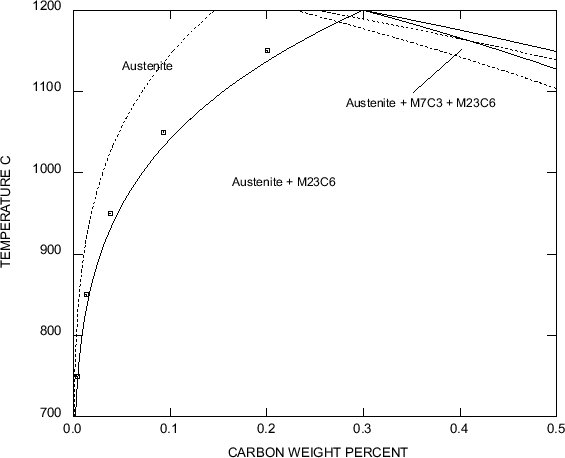 |
As can be seen in figure 5, this is valid for a typical
18/12
steel, but one should be careful as it is sensibly modified by the
chromium and nickel content. Increasing the chromium content reduces
the solubility of carbon
in austenite. It also increases the kinetics of
M23C6 precipitation, as does
an increase in carbon content: from 0.02 to 0.08C wt%, the nose of the C-curve
is shifted from 100 h to 0.1 h.
M23C6 first precipitates on grain boundaries, then, with increasing
time, on incoherent twin boundaries,
coherent twin boundaries and finally in the matrix on dislocations.
In the matrix, it forms as evenly spaced angular blocks.
At long ageing times, grain boundary carbides can form a completely
interlocked structure.
The kinetics of precipitation is affected by Mo, which stabilises
the carbide and accelerates its formation. On the other hand, nitrogen is
well-known to retard both formation and coarsening rates of
M23C6, and an
often proposed explanation is that nitrogen reduces the
diffusivity of Cr and C in the austenite [4], [9].
However, Degalaix and Foct [38] found that if the carbon content
was higher than 0.08 wt%, increasing the nitrogen content could have the
opposite effect.
More recent investigations indicate that N actually enhances the diffusion of
substitutional elements by increasing the formation of vacancies, but delays
the nucleation of
M23C6, the structure of which is destabilised when carbon is
partially substituted by nitrogen [8].
In a simple type 304 steel ,
M23C6 is often the only carbide found at any ageing
time. Although sometimes
M6C is found (Biss and Sikka, [39]),
it is as a minor phase and no mention is made of an instability of
M23C6
with regard to
M6C. When molybdenum is added (type 316),
M23C6 can
partially transform to
M6C (see further); it is however always reported
that
M23C6 remains the main carbide even after long ageing. In fact,
M23C6
and
M6C also coexists in the X5CrNiMo1713 (17Cr, 13Cr, 5Mo wt%) studied
by Thier et al. [40].
This is not the case when niobium is involved in the formation of
M6C,
which seems then more stable and becomes the dominant carbide at long ageing
times [41].
In stabilised grades, the situation is much more complex: from the
literature found, it is not possible to state clearly whether
M23C6 is
sometimes first formed or always follows MX precipitation, nor which phase is
the more stable on long term ageing.
Thorvaldsson and Dunlop
([24],[42],[43]), studying the effect of
different stabilising elements and
their combinations, found that
M23C6 was more stable than TiC, but less than
NbC. This is consistent with Grot and Spruiell [44], who found
formation of
M23C6 in a type 321 after long term ageing,
and with Kikuchi et al.
[9] for a 20/25. These authors concluded that TiC retards the
precipitation of
M23C6 but does not suppress it.
On the other hand, Bentley and Leitnaker [45],
studying a type 321 steel having been in service for 17 years at 600
C
did not find any
M23C6 and
concluded that TiC was more stable. Lai [46] observed no
M23C6 in a
type 321 used up to rupture (16000-29000 h at 600
C).
Obviously, considerations on the relative stability of the two
phases only make sense if the titanium content is enough to combine all
carbon present, as in the opposite case,
M23C6 forms with the excess carbon.
The studies in which
M23C6 formation appears as an anomaly deal with steels in
which Ti content is higher or equal than that required for full stabilisation.
The agreement is better for NbC, which is more stable than
M23C6. However,
M23C6 can form as a transient phase.
M6C is also known as
-carbide, but will be referred to as
M6C
to avoid confusion with
-phase (Laves phase).
It
generally refers to a phase of very variable composition. In most cases, it is
formed only after long ageing times, and therefore is quite little documented.
Moreover, its appearance and disappearance are strongly linked to that of
other constituents and it is difficult to give it any absolute position
in a TTP (Time Temperature Precipitation) diagram.
M6C is a diamond-type fcc carbide whose lattice parameter varies between
10.95 and 11.28 Å. Its space group is Fd3m, which distinguishes it
from
M23C6 and G-phase which both are fcc of similar lattice parameters,
but have a Fm3m space group. The
-carbide structure is described
by Stadelmaier in [47] for example. This structure encompasses a
wide range of compositions and only the one which are commonly found in creep
resistant austenitic stainless steels will be reviewed here.
M6C composition can be molybdenum-rich
(
(FeCr)21Mo3C6)
or niobium-rich (
Fe3Nb3C). The
molybdenum rich
Fe3Mo3C (a=11.11 Å)
was reported in high Mo steels, but never in austenitic
steels [48]. Instead, a fraction of molybdenum is replaced by iron
or chromium, and the lattice parameter is reduced (a=10.95 Å)
[48]. The composition reported by Brun et al. [49]
in a 316 steel containing Ti shows substantial amounts of Ni also
dissolving in
M6C (see table 4).
Table:
Composition of
M6C as measured by Brun et al. in a
316 steel containing titanium.
Si at% |
Mo at% |
Ti at% |
Cr at% |
Mn at% |
Fe at% |
Ni at% |
4.5 |
6.5 |
0.8 |
30 |
0.5 |
26.7 |
31 |
|
Silicon has
been reported to dissolve in this phase to form
M5SiC, but such a phase is very seldom found.
Other elements which can be included in the general notation
M are Ni, Ti, Co. In NF-709 (a 20/25 Nb stabilised, with 0.17N wt%),
long-term ageing allows formation of
Cr3Ni2SiC; such a composition has
been reported by Williams et al. in a study of irradiated type 316
(1984,[50]) and by Titchmarsh et al. in a similar steel
(1981,[51]), at rather low temperatures (466
C) but not above
670
C.
Its formation in such steels is linked with the segregation
effects caused by irradiation, in particular the Si segregation to point
defect sinks.
This particular composition has a lattice parameter of 10.62Å
(JCPDS 17-330),
which makes it extremely similar to
M23C6 from a structural point of view.
Although always referred to as
Cr3Ni2SiC, its actual composition
includes substantial amounts of Mo and Fe (see table 5),
the concentrations of which increase with temperature (Williams,[50]).
Williams therefore proposed the more general formula
(Cr,Mo)3(Ni,Fe)2SiC.
Jargelius-Peterson [52] found a nitrogen rich similar phase (
Cr3Ni2SiN)
after furnace ageing of a 20Cr25Ni5Mo0.2N steel. It is reported after 5h and
3000 h at 850
C, therefore being probably an equilibrium phase. In
agreement with the observation that the Mo content increases with temperature,
the composition found here includes as much as 25 wt% Mo (this is also due
to the larger Mo content of the alloy).
In a type 316 steel, the composition of
M6C is close to
(FeCr)21Mo3C6. Weiss and Stickler
[48] proposed that it formed as follows
It is not reported by Minami et al. [41] after 10000 h at 750
C
(instead,
-phase is found), neither by Lai and Meshkat [53]
after 10000 h at 600 and 650
C, nor by Barcik [54]
for the same time, up
to 900
C. However, it was found by Stoter [55] in specimen
of 316 having been in service at 650
C for 28000 and 60000 h, in
very small amounts and always associated with
M23C6.
Nitrogen seems to have a large influence on
M6C formation:
Thier et al. [40] did not find this carbide after 1000 h in a type
316 with 0.037N wt%, but found it after only 1 h ageing at 900
C when
the nitrogen content was 0.069 wt%. Gavriljuk and Berns [8]
suggest that the calculations performed by Jargelius-Petterson [56]
raise controversy, as she shows that an increase of nitrogen in a 20Cr,
25Ni, 4.5Mo wt% steel reduces the
driving force for
M6C. However, one must notice that
M6C is quite
poorly described in the SGTE databases, as it only contains information about
the Mo rich carbide, that is to say it describes only one of the possible
compositions of the
-structure. In this regard, it is possible to say
that the
-structure is in both cases stabilised but with different
compositions. In particular, Jargelius-Petterson [56] reports that
M5SiN is always present and favoured by high nitrogen
contents. It seems therefore that nitrogen generally stabilises the
-structure, but the composition of this phase varies with the alloy.
In type 321 (Ti-stabilised), none of the studies found
report
M6C.
In type 347, on the contrary, the presence of Nb seems to promote
the formation of a niobium rich
M6C. Care should be taken as Powell et al.
[57] have given sensible arguments showing that G-phase
and
M6C had often been mistaken. However, if the structures are very
similar, the composition
should differentiate clearly
Fe3Nb3C or
Cr3Ni2SiC (as in NF709) from
Ni16Nb6Si7.
The experimental methods must be linked with the results of the different
studies. In general, Nb-rich
M6C seems to form only on long-term ageing.
Kikuchi et al. [9] do not report it after 1000 h at 700
C in a
20/25. In a 18/8 steel, it is reported between 600 and 800
C
by Minami et al.
[41] at very long time (
50000 h) for 600
C
but faster (
2000 h) for 800
C.
They proposed a sequence illustrated in fig 6.
Figure:
Precipitation sequence leading to
M6C when Nb is
in excess, as proposed by Minami et al. in [58]
 |
This mechanism implies excess of Nb is present. If Nb is less than that
required for
combination of all carbon, no such phase is observed (Steel Tempaloy A1 in
[41], similar to a 304 with 0.13Nb, 0.06Ti, 0.07C wt%)
In 20/25 alloys, as written above,
M6C and G-phase have probably
been often mistaken (e.g. [59]) in early studies where identification
relied on X-ray or electron diffraction only. It is difficult to conclude which
phase forms preferentially: Ramaswamy et al. [60] report
M6C in a
20/25 with low Si content (0.03 wt%), but other studies report G-phase (Si
content 0.4-0.7 wt%).
When nitrogen is present (in 347 or in 20/25) in sufficient quantities,
Z-phase forms and it is difficult to have an idea of its stability with regard to
M6C.
G-phase, which is considered further, is an alternative Si rich
phase to
Cr3Ni2SiC.
As mentioned above, the composition
Cr3Ni2SiC is very seldom reported in the
literature. Titchmarsh and Williams have reported its formation in
irradiated steel of composition close to that of 316 with addition of 1.8wt% Nb.
They noted [51] and provided evidence [61] that G-phase formed
preferentially only when carbon was not available.
In 20/25-Nb-C steels though, Powell et al. (1984 [62],
1987 [57]) and Ecob et al. (1987 [63]) have found G-phase
and observed that NbC partially transforms to G-phase with time. It seems
reasonable to propose that in 20/25, G-phase is stabilised with regard
to
Cr3Ni2SiC, probably because of the larger Ni content.
However, in NF709 [5]
(composition in table 1),
Cr3Ni2SiC is reported. This is
inconsistent with the
studies quoted above which seem to indicate G-phase as a more stable phase. It
is not clear however whether the presence of carbon or nitrogen
was investigated or
the composition
Cr3Ni2SiC assumed. Investigations of the exact nature of this
precipitate are required to determine whether it is a nitride or a carbide.
A nitride would be expected as it would not be incoherent with the former
observations that G-phase is more stable than
Cr3Ni2SiC and that the
-structure
is stabilised by nitrogen.
Intermetallic phases
Sigma phase is a well-known intermetallic phase which forms in the
Fe-Cr system, with a composition FeCr. In highly alloyed steels, its
composition is variable. Its precipitation is associated with embrittlement. In
creep resistant steels, it has a detrimental effect on creep properties when
precipitated on grain boundaries, but little effect when it precipitates
intragranularly.
Sigma has a tetragonal unit cell (space group P42/mnm) with a=8.80 Å
and c=4.54 Å (FeCr). This unit cell contains 30 atoms.
Reported orientation relationships are [4]:
The composition varies quite widely and it is difficult to give a formula.
For example, Jargelius-Petterson [56]
reports the following range of composition for
sigma in a 20/25 with Mo content varying between 4.5 and 6.0 wt%:
|
Si |
Cr |
Mn |
Fe |
Ni |
Mo |
wt% |
0-1 |
27-32 |
1-9 |
35-43 |
8-15 |
10-16 |
for a type 316 [36], a typical composition is (other elements not given):
An in-depth review of
-phase precipitation in Cr-Ni austenitic steels
has been done by Barcik [64].
Sigma phase precipitates first on triple points then on grain faces. After
long term ageing at high temperature, it also forms on incoherent twin
boundaries and intragranular inclusions.
The mechanism of nucleation is still a matter of controversy, particularly
on the role of
-ferrite and
M23C6 in the nucleation process.
Studies have reported its formation
associated with the dissolution of
M23C6, but also independently [4].
It is found in most of the grades of austenitic stainless steels: type 304, 316 (Mo), 321 (Ti stabilised) and 347 (Nb stabilised) (see for example [41]).
However, it forms after different times. The 25Cr-20Ni steels can exhibit as
much as 20 wt% of
-phase.
Figure:
Precipitation of sigma in different grades of austenitic stainless steels.
Tempaloy-A1 is an 18/10 with a Nb/C ratio of 1.86, whereas the 347 has a ratio
of 17.40. The percentage is the area etched by KOH. After [41]
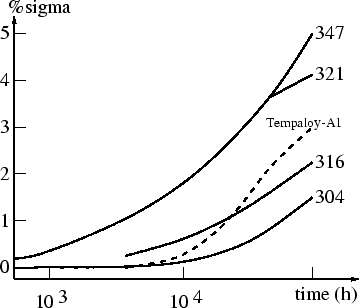 |
In stabilised grades, its formation is
faster than in other grades: Minami et al. report precipitation of
after
1000 h at 700
C in 347 and 321
(347 precipitating
slightly faster
than 321). In 304, 316 and Tempaloy-A1,
phase is found in significant
quantities only after 10000 h (fig 7).
It is worth noting that Tempaloy-A1 is Nb
stabilised, but with a Nb/C ratio of 1.86, while this ratio is
17.40 in the 347.
This correlates well with the fact that
forms when the carbon content
falls below a critical value when the chromium equivalent is higher than 18wt%.
In the 347, almost all the carbon is rapidly precipitated as NbC, while the low
Nb content of Tempaloy-A1 leaves some carbon in solution.
The different trend for 321 could be linked to the instability of TiC with
regard to
M23C6. The precipitation of
M23C6 lowers both the carbon and the
chromium content.
The results of Grot and Spruiell [44] show on the contrary no sigma
phase forming up to 2000 h in a type 321.
-phase is also found in 20/25 (fig 8).
Different factors affect the formation of sigma phase. Elements like Cr, Nb, Ti
or Mo are known to promote
formation. Silicon promotes and accelerates
its formation. In general, the formation of sigma in austenite is about 100
times slower than in ferrite. Consequently, the presence of
-ferrite
accelerates sigma precipitation. [64]
A method has been developed by Woodyatt et al. [4] to estimate
the
-forming
tendency of an alloy, based on the electron vacancy number
:
If
is higher than 2.52, the alloy should form
.
Laves phase is found in various grades of austenitic stainless steels. It is
often a minor constituent. It precipitates intragranularly in the form of
equiaxed particles, occasionally on grain boundaries [48]. Whether
Laves phase has a detrimental effect or not on creep properties is still
discussed. In niobium stabilised steels however, it is likely that Laves phase
are detrimental because they allow formation of
M6C (see below).
Laves phase is a
hexagonal phase of space group P63/mmc, with a=4.73 Å and
c=7.72 Å. The main factor determining its formation being the relative atomic
size of the constituent atoms, the ranges of composition are quite
small.
Jargelius-Petterson [56] measured the following composition
for Laves phase in a 20/25 with 5Mo wt%:
After 10 min at 850 C |
|
Fe |
Mo |
Cr |
Ni |
Mn |
Si |
wt% |
 |
 |
 |
 |
 |
 |
After 3000 h at 850 C |
wt% |
 |
 |
 |
 |
 |
 |
This shows that Laves phase probably does not form at its exact equilibrium
composition. In stabilised grades,
Fe2Nb or
Fe2Ti (more seldom) can form.
Denham et al. (1969, [65] proposed for
Fe2Nb the following orientation relationships:
In type 304, Laves phase is not found, due to the absence of Mo, Nb or Ti. In
type 316, which contains typically 2-2.5Mo wt%, it is found after relatively
long ageing times: Minami et al. [41]
report its formation after a minimum of 1000 h,
between 625 and 800
C.
The
experimental results of Lai [66] are in agreement with the
dissolution of
Fe2Mo above 800
C. Coherently,
White and Le May [67] do not report any Laves phase precipitation
between 640 and 800
C for ageing times up to 900 h. Weiss and Stickler
[48] report a slightly higher maximum temperature for Laves
precipitation in type 316 as they found it up to 815
C. Its formation
interacts in a competitive way with that of
and
phases.
For example, the presence of
-ferrite delays its formation because it
enhances that of
and
phases.
In titanium stabilised grades, the formation of
Fe2Ti
is never reported in compositions similar to that of a 321 steel.
Minami et al. do not report it for ageing times up to
50000 h between 600 and 750
C, in a type 321.
However, it is found by Beattie and Hagel [68] in a A286 type alloy, containing 16Cr, 26Ni and 1.8Ti wt%, after 1000 h at 815
C.
This is directly related to the large amount of Ti used in such steels
compared to a typical 321.
In niobium stabilised steels,
Fe2Nb is frequently
reported after long ageing times, but as a transient phase which disappear for
Fe3Nb3C.
It is reported to form in a type 347 with
0.87Nb and 0.05C wt%, after 1000 h between 650 and 800
C, and
disappear after 5000-10000 h [41]. However, its formation is
dependent on the availability of niobium. In the same study, the Tempaloy-A1
(18/10 with 0.13Nb for 0.07C wt%) do not precipitate Laves phase after
ageing treatments up to 25000 h. Instead, only NbC is found (see figure
6). The same results are reported by Raghavan et al.
[21], who found NbC and Laves phase in a type 347 with 0.8Nb and
0.07C wt% (8000 h at
600
C), but only Z-phase in a
modified 347 with
0.3Nb and 0.09N wt%. It is therefore probable that both NbC and Z-phase
are more stable than
Fe2Nb.
phase is most of the time a minor intermetallic phase. It is mainly
found in type 316 above 750
C
phase is a bcc (body-centered cubic)
phase of space group
. The unit cell
contains 58 atoms and has a lattice parameter varying between 8.807 and
8.878 Å.
A typical composition is
Fe36Cr12Mo10
but the phase has a high tolerance for metal interchanges. The structure has
large holes which allow presence of carbon, sometimes making this phase
better described as a
M18C carbide.
It nucleates on
grain boundaries, incoherent twin boundaries but also intragranularly on
dislocations.
Although it is sometimes (but seldom) present in very small quantities in 321
[44],
phase is only a significant phase in type 316, when
the ageing temperature is high enough. For example,
it is reported by Minami et al. for times up to 25000 h and temperatures
between 700 and 850
C, and by Lai et al., as being the main phase with
between 715-850
C for times up to 5000 h, but not by Stoter
[55] after 28000 and 60000 h at 650
C.
G-Phase is a silicide forming in austenitic stainless steels stabilised with Ti or Nb.
It has been first reported by Beattie and Versnyder in 1956, in a A286 type
steel, that is a precipitation-hardening 26Ni-15Cr with variable
(0 to 2.3wt %) Ti and Al contents.
It has long been believed to form only under irradiation in
steels of the 300 series and in 20/25 steels.
However, Powell et al. showed, in 1985 [57] that it formed under
normal ageing in 20/25 Nb stabilised alloys, in the temperature range
500-850
C, and suggested that it had been identified as
M6C in earlier
studies of the same steel.
G-Phase has a general formula
A16D6C7 where A and D are transition
elements, and C a group IV element [63]. A is usually nickel, D
niobium (ref [57],[62],[63]) or titanium
[46].
Ecob et al. [63] mentioned the possibility of substitution, in
small quantities, of D (ie Nb or Ti) by Fe or Cr, and Powell et al.
[57] measured the following composition:
Table:
Composition of G-Phase measured in [57]
|
Ni |
Nb |
Si |
Fe |
Cr |
Wt% |
51 |
29 |
14 |
4.5 |
1.5 |
|
Lai found a titanium containing G-phase in a type 321 steel, and gives
a composition sensibly richer in nickel (table 7).
Table:
Composition of G-Phase measured in [46]
|
Ni |
Ti |
Si |
Fe |
Cr |
Wt% |
63.3 |
20.9 |
12.2 |
3.47 |
0.13 |
|
Note that none of these compositions clearly shows substitution of D when
trying to match the stoichiometric formula.
G-Phase has a fcc structure with a lattice parameter of
11.2 Å, this
corresponds to a content of 116 atoms per unit cell. The space group for
this structure is Fm3m.
It is remarkable that the lattice parameter seems to be the same for
Ni16Nb6Si7
(see [57],[62]) and
Ni16Ti6Si7 (see
[46],[68]). In a earlier study, Sumerling et al.
[59], studying a 20/25 Nb stabilised steel, found a lattice
parameter of
Å for a phase they identified as
M6C .
As mentioned before, Powell et al. have suggested that G-Phase was
identified as
M6C in early works on 20/25 Nb steels, because of close
compositions and structures. A detailed investigation of the structure
is sufficient to solve the problem (Ecob et al.,[63]), but additional
evidence has been sought by the use of EELS (Electron Energy Loss
Spectroscopy) (as in [57]) or a wavelength-dispersive crystal
spectrometer in SEM (as in [46]), both techniques making possible
quantitative measurements of light elements (C,N). These studies have confirmed
the absence of interstitial elements in G-Phase.
The general features of G-Phase formation are:
- It forms very predominantly on grain-boundaries (from where its name)
- It is now clear that it forms in 20/25 Nb stabilised steels and to an
extent which depends on the Si content.
- It has also been reported in a type 321 steel, but other results are
contradictory.
In one of the first studies on G-Phase
(Beattie and Hagel,[68])
the Ti rich G-phase is reported in a A286 type steel. It is not clear in what
conditions of temperature and time it forms, as it was often found to resist
the solution-treatment. However, G-Phase was not found in the alloy
containing only 0.01Si wt%, but formed at higher contents, and the volume
increased with the Si content. Adding 2 wt% of Al suppressed the formation
of G-Phase. This work also included a
steel in which the Ti content is more similar to that used in the 300 series, and
no G-phase was found.
The only report found of Ti rich G-phase in type 321
has been quoted above (Lai, [46]). Three out of seven type 321 steels
show G-phase after 16000h and 50000h at 600
C. The common factors between
the three type 321 steels which are found to form Ti rich G-phase in this study
are their small grain sizes and an excess of Ti with regard to the amount of
carbon present. However, in similar conditions, other studies (Minami et al.,
[41]; Bentley et al. [45]) do not report G-phase.
In 20/25-Nb-C stabilised steels, it is now clear that G-Phase can
form (see [57], [63], [62]) and, following the
suggestion of Powell et al., the works of Sumerling et al. and Dewey et al.
may be regarded as other evidences for G-Phase formation if one accepts
that
M6C must be read as G-Phase. In [59], in particular, the
authors measured a lattice parameter of
Å which
is much closer to the G-Phase parameter.
Figure:
TTP diagram from Powell et al. [57]
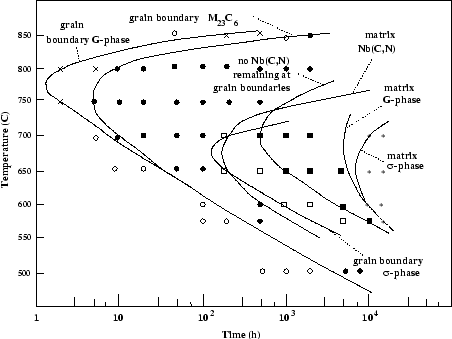 |
Powell et al. summarised their work in a TTP (Time Temperature
Precipitation) diagram shown in fig 8.
In their alloy (0.68Nb, 0.037C, 0.61Si wt%), G-Phase forms between
500 and 850
C, first on residual grain boundary particles of NbC, and
only after very long ageing on NbC particles in the matrix. The authors
propose that this is due to the easier diffusion of required elements in
the grain boundaries.
Ecob et al. [63], comparing the occurrence of G-Phase
in similar 20/25-Nb stabilised steels, noticed that alloys apparently similar
in composition exhibited different relative stabilities of NbC with regard to
G-Phase. They found that
an increase in the oxygen content led to a greater instability of NbC with
regard to G-Phase, and proposed that oxygen and silicon are involved in
a co-segregation process, a greater amount of oxygen segregating around NbC
leading to a greater segregation of Si in the same way. The silicon rich
region is more favorable to G-Phase formation.
In 20/25-Nb-N steels however, as it has been discussed in the section
regarding
M6C, it seems that
Cr3Ni2SiN forms preferentially to G-phase. No
results could be found that support this hypothesis.
In common 18/12-Nb steels, G-phase seems to be found only under
irradiation (Titchmarsh and Williams [51], Williams [50]).
Increasing the Si content to 6 wt% resulted in the formation during
furnace ageing of Nb G-phase, although provided that carbon was not available
to form
Cr3Ni2SiC. However, no study has been found which report niobium
G-phase in ordinary 18/12 steels.
Precipitates such as
Ni3Ti,
Ni3(Ti,Al), are only found in a particular class of
austenitic stainless steels: the precipitation hardening ones. A typical steel in
this category is A286, a 15Cr-25Ni-Al-Ti steel. They contain titanium and
aluminium in quantities substantially larger than the 300 series and related
compositions, to form
or other Ni, Ti, Al precipitates, as summarised in figure
9.
Figure:
Effect of aluminium and titanium on the equilibrium
phases present at 800
C in 15Cr-25Ni austenitic steels, from [69]
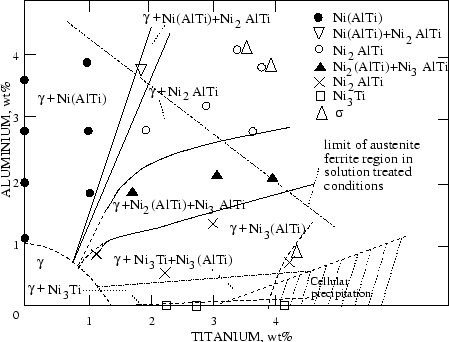 |
However, there are very few studies in which the creep properties of these steels
are given attention, and long term informations are not available (see for
example [70]). For this reason and because the precipitation in these
steels has been reviewed in [71], [69], it has been decided not
to cover in depth these precipitates.
These are [71]:
-
is a fcc
Ni3Al or
Ni3(Ti,Al) intermetallic compound of lattice parameter
3.60 Å. It is also the transition structure of
Ni3Ti.
is hexagonal (a=5.09 Å c=8.32 Å) and is the equilibrium
structure of
Ni3Ti.
is NiAl, formed at lower temperatures (up to 700
C) and short
ageing times (10-100h).
Attention has been concentrated on precipitates most often reported and
studied in creep resistant austenitic stainless steels.
However, other phases are sometimes reported depending on the alloying elements.
It forms in non-stabilised austenitic stainless steels with high nitrogen (0.2 wt% at 900
C with 20Ni wt%) [38]. It has a hcp (hexagonal close-packed) unit cell
of lattice parameters a=4.78 Å and c=4.44 Å [4]. Although an
major precipitate in high nitrogen non stabilised steels, it is not in either
nitrogen-bearing non-stabilised creep resistant austenitic stainless steels because of the lower N
content used, or in stabilised nitrogen bearing grades, because Z-phase seems
to form preferentially. A detailed review of this precipitate can be found in
[8].
It is reported by Jargelius-Petterson [56], [52] to form
in a non-stabilised 20/25 steel with 0.21N wt%. The composition after 10 min
at 850
C is:
|
Si |
Mn |
Cr |
Ni |
Mo |
Fe |
wt% |
1.0 0.2 |
1.1 0.3 |
47 1 |
20 1 |
13 1 |
19 1 |
It has a cubic structure of lattice parameter
a=6.3 Å [52].
The titanium carbosulphide
Ti4C2S2
is reported by Lai [46] in different type 321 steels aged at
600
C for times between 16000 and 53000 h, and by Minami et al.
[41] in
a similar steel, they precise that this phase is already present in the solution
treated condition. It has a hcp structure of lattice parameter a=3.21 Å
and .
Few data are available concerning the effect of copper in creep resistant
austenitic stainless steels. Tohyama et al. [72] used 3 wt% copper in Tempaloy-A1,
a steel similar to 347, with addition of a small amount of titanium.
This results in precipitation of a copper rich phase, independently of the
precipitation of other precipitates. The creep rupture strength is
significantly increased in comparison to the original composition.
The chromium phospide
Cr3P has been reported by
Rowcliffe et al.[73], in a 18/10 steel with 0.3 wt% P. It has a
tetragonal unit cell with a=9.186Å and c=4.558Å.
An attempt has been here made to review the characteristics of the main
precipitates found in austenitic stainless steels. Whereas the early stages of
precipitation are quite well understood in the usual grades of austenitic steels,
this is far from the case for the new generations of nitrogen-bearing stabilised
austenitic steels. There is a dirth of knowledge about the phases which
precipitate during long term ageing, particularly with respect to thermodynamic
data.
Z-phase, which plays an essential role in recent creep-resistant
austenitic or ferritic stainless steels, is not present in the SGTE databases
commonly used with thermodynamic calculation packages such as MT-DATA or
ThermoCalc. The kinetics of its formation are also rather obscure.
In discussing the stability of
M6C, there is some confusion
which arises from the fact that this phase is most often referred to as one
particular composition of the eta structure rather than the eta-structure
itself. Similarly, thermodynamic data are only available for the Mo-rich pole
of the eta structure. Other important compositions which are not present in
the SGTE databases include
Fe3Nb3C and
Cr3Ni2SiX.
The formation of MX precipitates is well documented, but again,
thermodynamic data are missing to model the solubility of Cr, which is likely to
be important in the kinetics of precipitation.
An assessment of the Cr-Nb-N system could help improving the description of NbX
precipitates, and would also provide thermodynamic data for Z-phase.
I am grateful to David Gooch of National Power, who funded the project this
literature review is part of. I am also thankful to Professor Alan Windle of
the university of Cambridge for provision of laboratory facilities, and to my
supervisor, Professor H.K.D.H. Bhadeshia, for his support, enthusiasm and
fruitful discussions.
Table 8:
Crystal structure and composition of the main precipitates in
austenitic stainless steels
Precipitate |
Structure |
Parameter (Å) |
Composition |
NbC |
fcc |
a=4.47 |
NbC |
NbN |
fcc |
a=4.40 |
NbN |
TiC |
fcc |
a=4.33 |
TiC |
TiN |
fcc |
a=4.24 |
TiN |
Z-phase |
tetragonal |
a=3.037 c=7.391 |
CrNbN |
M23C6 |
fcc |
a=10.57-10.68 |
Cr16Fe5
Mo2C (e.g.) |
M6C |
diamond cubic |
a=10.62-11.28 |
(FeCr)21Mo3
C;
Fe3Nb3C;
M5SiC |
Sigma |
tetragonal |
a=8.80 c=4.54 |
Fe,Ni,Cr,Mo |
Laves phase |
hexagonal |
a=4.73 c=7.72 |
Fe2Mo,
Fe2Nb |
-phase |
bcc |
a=8.807-8.878 |
Fe36Cr12
Mo10 |
G-Phase |
fcc |
a=11.2 |
Ni16Nb6
Si7,
Ni16Ti6
Si7 |
|
- 1
-
Pickering F. B.
Physical Metallurgical Development of Stainless Steels.
In Proc. Conf. Stainless Steels 84, Gothenburg, Sept 1984,
pages 2-28, 1984.
- 2
-
MT-DATA.
National Physical Laboratory, Teddington, Middlesex, U.K., 1989.
- 3
-
Lacombe P., Baroux B., and Beranger G., editors.
Stainless Steels.
Les Editions de Physiques, Les Ulis, 1993.
- 4
-
Marshall P.
Austenitic Stainless Steels, Microstructure and Mechanical
Properties.
Elsevier, London, 1984.
- 5
-
Nippon Steel Corporation.
Quality and Properties of NF709 Austenitic Stainless Steel for
boiler tubing applications.
Technical report, Nippon Steel Corporation, 1996.
- 6
-
ASM International.
Irons, steels and high performance alloys.
In Davis J.R., editor, Metals Handbook, volume 1. 1990.
- 7
-
Naylor D.J. and Cook W.T.
Materials Science and Technology, volume 7.
VCH Publishers Inc., 1992.
- 8
-
Gavrilnjuk V.G. and Berns H.
High Nitrogen Steels.
Springer, 1999.
- 9
-
Kikuchi M., Sakabibara M., Otoguro Y., Mimura M., Takahashi T., and Fujita T.
An Austenitic Heat Resisiting Steel Tube developed for Advanced
Fossil Steam Plant.
In International Conference on Creep, Tokyo, April 14-18,
1986, pages 215-220, 1986.
- 10
-
Rios P.
Expression for Solubility Product of Niobium Carbonitride in
Austenite.
Mater. Sci. Techn., 4:324-327, 1988.
- 11
-
Rios P.
Method for Determination of Mole Fraction and Composition of a
Multicomponent f.c.c. Carbonitride.
Mater. Sci. Eng., 142:87-94, 1991.
- 12
-
Heilong Z. and Kirkaldy J. S.
Thermodynamic Calculation and Experimental Verification of the
Carbonitride-Austenite Equilibrium in Ti-Nb Microalloyed Steels.
Metal. Trans. A, 23:651-657, 1992.
- 13
-
Hughes H.
Complex Nitride in Cr-Ni-Nb Steels.
J.I.S.I., pages 775-778, 1967.
- 14
-
Andrén H. O., Henjered A., and Karlsson L.
MX Precipitates in Stabilized Austenitic Stainless Steels.
In Proc. Conf. Stainless Steels 84, Gothenburg, Sept 1984,
pages 91-96, 1984.
- 15
-
Andrén H. O., Henjered A., and Norden H.
Composition of MC Precipitates in a Titanium Stabilised Stainless
Steel.
J. Mater. Sci., 15:2365-2368, 1980.
- 16
-
Wadsworth J., Woodhead J. H., and Keowm S. R.
The Influence of Stoichiometry upon Carbide Precipitation.
Metal Sci., pages 342-348, 1976.
- 17
-
Keown S. R. and Pickering F. B.
Effect of Niobium Carbide on the Creep Rupture Properties of
Austenitic Stainless Steels.
In Creep strength in steel and high-temperature alloys, pages
229-234, 1974.
- 18
-
Adamson J. M. and Martin J. W.
Tertiary Creep Processes in 20%Cr, 25%Ni Austenitic Stainless
Steels of differing Nb/C Ratios.
J.I.S.I., pages 271-275, 1972.
- 19
-
Jack D. H. and Jack K. H.
Structure of Z-Phase.
J.I.S.I., pages 790-792, 1972.
- 20
-
Vodárek V.
Morphology and Orientation Relationship of Z-phase in Austenite.
Scripta Metall. Mater., 25:549-552, 1991.
- 21
-
Raghavan A., Klein C. F., and Marzinsky C. N.
Instabilities in Stabilized Austenitic Stainless Steels.
Metall. Trans. A, 23:2455-2467, 1992.
- 22
-
Robinson P. W. and Jack D. H.
Precipitation of Z-Phase in a High-Nitrogen Stainless Steel.
In Lula R., editor, New Developments in Stainless Steel
Technology, pages 71-76. Amer. Soc. Metals, 1985.
- 23
-
Vorádek V.
Effect of Niobium on the Microstructure and Creep Properties of AISI
316LN type steels.
In Nordberg H. and Björklund J., editors, Applications of
Stainless Steels '92, volume 1, pages 123-132. Jernkontoret and Avesta
Research Foundation and ASM ineternational, 1992.
- 24
-
Thorvaldsson T. and Dunlop G. L.
Effect of Stabilizing Additions on Precipitation Reactions in
Austenitic Stainless Steel.
Metal Sci., 16:184-190, 1982.
- 25
-
Knowles G.
The Creep Strength of a 20%Cr-25%Ni-Nb Steel Containing Controlled
Particle Dispersions.
Metal Sci., pages 117-122, 1977.
- 26
-
Uno H., Kimura A., and Misawa T.
Effect of Nb on Intergranular Precipitation Behavior of Cr Carbides
in N-bearing Austenitic Stainless Steels.
Corrosion, 2(6):467-474, 1992.
- 27
-
Beckitt F.R. and Clarck B.R.
The Shape and Mechanism of Formation of
M23C6 Carbide in Austenite.
Acta Metall., 15:113-129, 1967.
- 28
-
Lewis M.H. and Hattersley B.
Precipitation of
M23C6 in Austenitic Steels.
Acta Metall., 13:1159-1168, 1965.
- 29
-
Tanaka H., Murata M., Abe F., and Yagi K.
The Effect of Carbide Distributions on long-term Creep Rupture
Strength of SUS321H and SUS347H stainless steels.
Mater. Sci. Eng., A234:1049-1052, 1997.
- 30
-
Singhal L.K. and Martin J.W.
The Growth of
M23C6 on Incoherent Twin Boundaries in Austenite.
Acta Metall., 15:1603-1610, 1967.
- 31
-
Sasmal B.
Formation of lamellar
M23C6 on and near twin boundaries in
austenitic stainless steels.
Bul. Mat. Sci., 6:617-623, July 1984.
- 32
-
Sasmal B.
Mechanism of the Formation of
M23C6 Plates around undissolved NbC
Particles in a Stabilized Austenitic Stainless Steel.
J. Mater. Sci., 32:5439-5444, 1997.
- 33
-
Ägren J.
Computer Simulation of Diffusional Reactions in Complex Steels.
ISIJ International, 32:291-296, 1992.
- 34
-
Van der Ven A. and Delaey L.
Models for the Precipitate Growth during the
Transformation in Fe-C and Fe-Mn-C Alloys.
Progress in Mat. Sci., 40:181-264, 1996.
- 35
-
Hättestrand and Andrén H.-O.
Boron distribution in 9-12% chromium steels.
Mater. Sci. Eng., A270:33-37, 1999.
- 36
-
Lai J. K. L.
A Review of Precipitation Behaviour in AISI Type 316 Stainless
Steel.
Mater. Sci. Eng., 61:101-109, 1983.
- 37
-
Deighton M.
Solubility of
M23C6 in Type 316 Stainless Steel.
J.I.S.I., pages 1012-1014, 1970.
- 38
-
Degalaix S. and Foct J.
Nitrogen in Austenitic Stainless Steels(I).
Mém. Rev. Métall., pages 645-653, 1987.
- 39
-
Biss V. A. and Sikka V. K.
Metallography Study of Type 304 Stainless Steel Long-Term
Creep-Rupture Specimen.
Metall. Trans. A, pages 1360-1362, 1981.
- 40
-
Thier H., Baumel A., and Schmidtmann P.
Effect of Nitrogen on the Precipitation Behaviour of the Steel X 5
CrNiMo 17 13.
Arch. Eisenhuettenwesen, 40:333-339, 1969.
- 41
-
Minami Y., Kimura H., and Ihara Y.
Microstructural Changes in Austenitic Stainless Steels during
Long-Term Aging.
Mater. Sci. Techn., 2:795-806, 1986.
- 42
-
Thorvaldsson T. and Dunlop G. L.
Precipitation Reactions in Ti-stabilized Austenitic Stainless
Steel.
Metal Sci., pages 513-518, 1981.
- 43
-
Thorvaldsson T. and Dunlop G. L.
The Influence of Composition on Precipitation in Stabilized
Austenitic Stainless Steels.
In Proc. Int. Conf. on The strength of metals and alloys, pages
755-760, 1979.
- 44
-
Grot A. S. and Spruiell J. E.
Microstructural Stability of Titanium-modified Type 316 and Type 317
Stainless Steel.
Metall. Trans. A, pages 2023-2030, 1975.
- 45
-
Bentley J. and Leitnaker J. M.
Stable phases in aged type 321 stainless steel.
In Collings E.W. and King H.W., editors, The Metal Sience of
Stainless Steels, pages 70-91. The Metallurgical Society of AIME, 1978.
- 46
-
Lai J. K. L.
Precipitate Phases in Type 321 Steel.
Mater. Sci. Techn., 1:97-100, 1985.
- 47
-
Stadelmaier H.H.
Metal-rich metal-metalloid phases.
In Plenum Press, editor, Development in the Structural Chemistry
of Alloy Phases, pages 141-180, 1969.
- 48
-
Weiss B. and Stickler R.
Phase Instabilities During High Temperature Exposure of 316
Austenitic Stainless Steel.
Metall. Trans A, 3:851-866, 1972.
- 49
-
Brun G., Naour J.L., and Vouillon M.
Etude de la microstructure d'un acier 316 au titane apres
vieillissement et apres irradiation aux neutrons.
J. Nucl. Mater., 101:109-123, 1981.
- 50
-
Williams T.M.
Precipitation in Neutron-Irradiated Type 316 Austenitic STeel.
In Institute of Metals, editor, Stainless Steels 84, pages
403-412, 1985.
- 51
-
Titchmarsh J.M. and Williams T.M.
Precipitates in Neutron-Irradiated Austenitic Stainless Steel .
In Lorimer G.W, Jacobs M.H., and Doig P., editors, Quantitative
Microanalysis with High Spatial Resolution, pages 223-228, London, 1981.
Institute of Metals.
- 52
-
R. F. A. Jargelius-Petterson.
Precipitation in Nitrogen-Alloyed Stainless Steel at 850
C.
Scripta Metall. Mater., 28:1399-1403, 1993.
- 53
-
Lai J. K. L and Meshkat M.
Kinetics of Precipitation of
-phase and
M23C6 Carbide in a
Cast Type 316 Stainless Steel.
Metal Sci., pages 415-420, 1978.
- 54
-
Barcik J.
The Kinetics of
-phase Precipitation in AISI 310 and AISI
316 Steels.
Metall Trans. A, pages 635-641, 1983.
- 55
-
Stoter L. P.
Thermal Ageing Effects in AISI Type 316 Stainless Steel.
J.Mater.Sci., pages 1039-1051, 1981.
- 56
-
R. F. A. Jargelius-Petterson.
Precipitation Trends in Highly Alloyed Austenitic Stainless Steels.
Z. Metallkd., pages 177-183, 1998.
- 57
-
Powell D. J, Pilkington R., and Miller D. A.
The Precipitation Characteristics of 20%Cr/25%Ni-Nb Stanilised
Stainless Steel.
Acta Metall., 36(3):713-724, 1988.
- 58
-
Minami Y., Kimura H., and Tanimura M.
Creep Rupture Properties of 18%Cr-8%Ni-Ti-Nb and Type 347H
Austenitic Stainless SteelS.
In Lula R., editor, New Developments in Stainless Steel
Technology, pages 231-242. Amer. Soc. Metals, 1985.
- 59
-
Sumerling R. and Nutting J.
Precipitation in a 20%Cr-25%Ni Steel Stabilized with Niobium.
J.I.S.I., pages 398-405, 1965.
- 60
-
Ramaswamy V. and West D. R. F.
NbC Precipitation in a 20%Cr-25%Ni-1%Nb Austenitic Steel.
J.I.S.I., pages 391-394, 1970.
- 61
-
Williams T.M. and Titchmarsh J.M.
Silicon rich phases in austenitic alloys.
J. Nucl. Mater., 98:223-226, 1981.
- 62
-
Powell D. J., Pilkington R., and Miller D. A.
Influence of Thermal Ageing on Creep Properties of a
20/25/Nb-stabilised Steel.
In Proc. Conf. Stainless Steels 84, Gothenburg, Sept 1984,
pages 382-390, 1984.
- 63
-
Ecob R. C., Lobb R. C., and Kohler V. L.
The Formation of G-phase in 20/25 Nb Stainless Steel AGR Fuel
Cladding Alloy and its Effect on Creep Properties.
J. Mater. Sci., 22:2867-2880, 1987.
- 64
-
Barcik J.
Mechanism of
-phase formation in cr-ni austenitic steels.
Mat. Sci. Techn., 4:5-15, 1988.
- 65
-
Denham A.W. and Silcock J.M.
Precipitation of
Fe2 Nb in a 16-wt%Ni
16-wt%Cr Steel, and The Effect of Mn and Si Additions.
J.I.S.I., pages 585-592, 1969.
- 66
-
Lai J. K. L.
A Study of Precipitation in AISI Type 316 Stainless Steel.
Mater. Sci. Eng., 58:195-209, 1983.
- 67
-
White W. E. and Le May I.
Metallographic Observations on the Formation and Occurence of
Ferrite, Sigma Phase, and Carbides in Austenitic Stainless Steels. Part II:
Studies of AISI Type 316 Stainless Steel.
Metallography, 3:51-60, 1970.
- 68
-
Beattie H. J. and Hagel W. C.
Intermetallic Compounds in Titanium-Hardened Alloys.
J. Metals, pages 911-917, 1957.
- 69
-
Pickering F.B.
Some aspects of the precipitation of nickel-aluminium-titanium
intermetallic compounds in ferrous materials.
In Pickering F.B., editor, The metallurgical evolution of
Stainless Steels, pages 391-401. The Metals Society, London, 1979.
- 70
-
Satyanarayana D.V.V., Pandey M.C., and Taplin D.M.R.
Creep behaviour of a precipitation hardenable austenitic stainless
steel.
Trans. Indian Inst. Met., 49(4):419-423, 1996.
- 71
-
Dulis E.J.
Age-hardening austenitic stainless steels.
In Pickering F.B., editor, The metallurgical evolution of
Stainless Steels, pages 420-441. The Metals Society, London, 1979.
- 72
-
Tohyama A. and Minami Y.
Development of the high temperature materials for ultra super
critical boilers.
In Viswanathan R. and Nutting J., editors, Advanced Heat
Resistant Steels for Power Generation, pages 494-506. IOM Communications
Ltd, IOM Communications Ltd, 1999.
- 73
-
Rowcliffe A.F. and Nicholson R.B.
Quenching defects and precipitation in a phosphorus-containing
austenitic stainless steel.
Acta Metall., 20:143-155, 1972.
This document was generated using the
LaTeX2HTML translator Version 2002 (1.62)
Copyright © 1993, 1994, 1995, 1996,
Nikos Drakos,
Computer Based Learning Unit, University of Leeds.
Copyright © 1997, 1998, 1999,
Ross Moore,
Mathematics Department, Macquarie University, Sydney.
The command line arguments were:
latex2html -split 1 -address 'Home' -title 'Review: precipitation in austenitic stainless steels' -white -noparbox_images -math_parsing -notop_navigation -nonavigation final
The translation was initiated by on 2003-07-25
Home