Parvez Mannan of the Noble Engineering Services, New South Wales in Australia, kindly agreed to make these images and associated information available.
The bearing inner race has the approximate chemical composition Fe-0.95C-0.45Si-1Mn-1.77Cr-0.52Mo-0.010P-0.004S wt%, together with traces of some other elements. The rolling elements have the approximate composition Fe-0.97C-0.31Si-0.75Mn-1.8Cr-0.15Mo-0.012P-0.001S wt%.
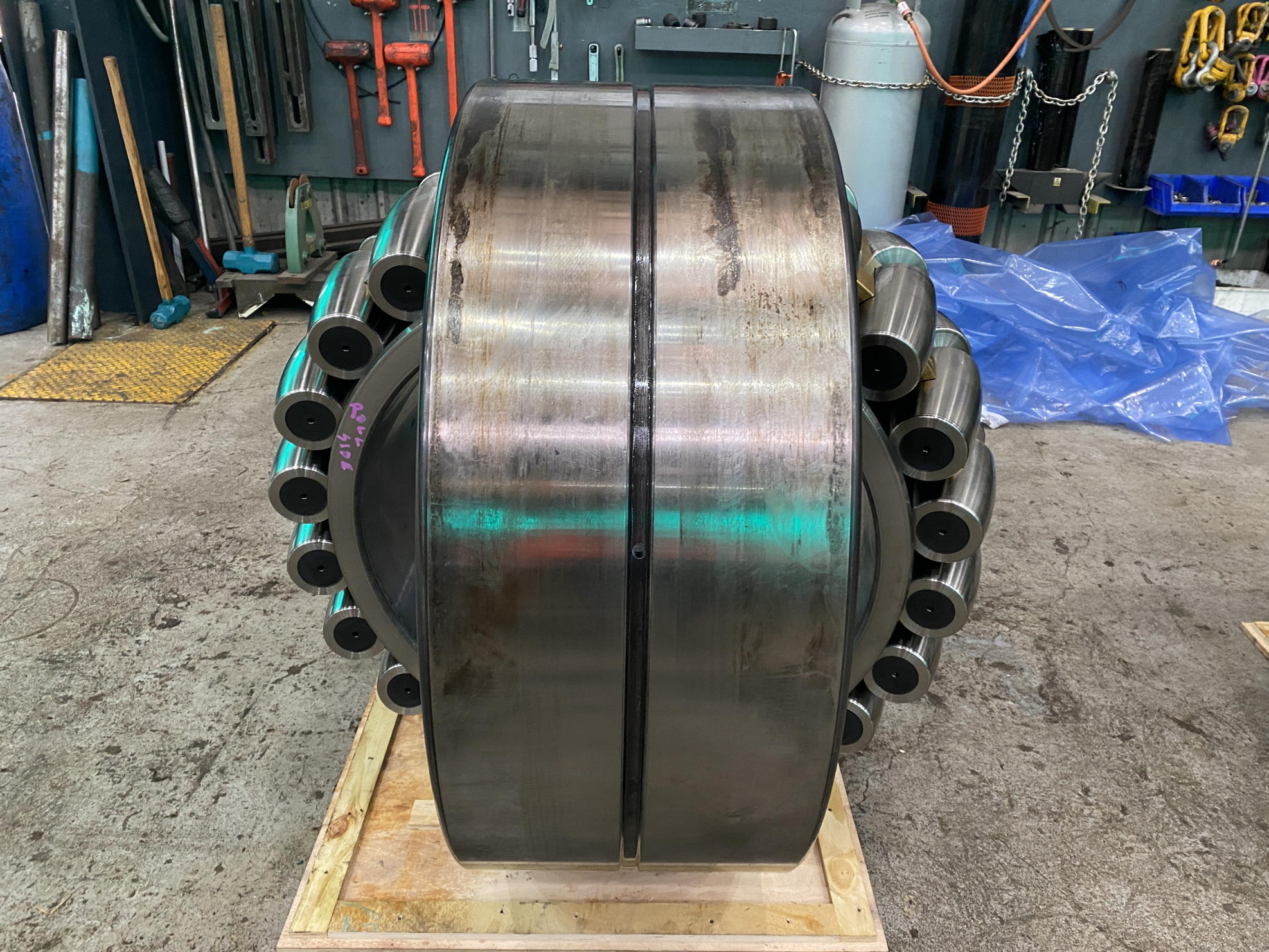 The bearing. |
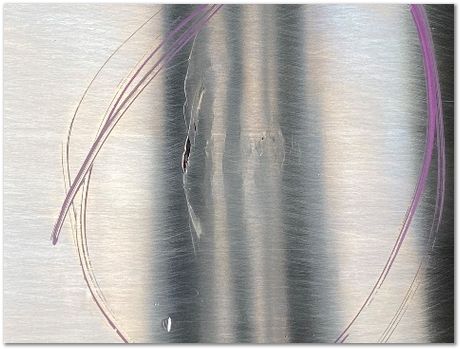 35 mm transverse crack associated with spalling, located 90 mm from the edge of the raceway. |
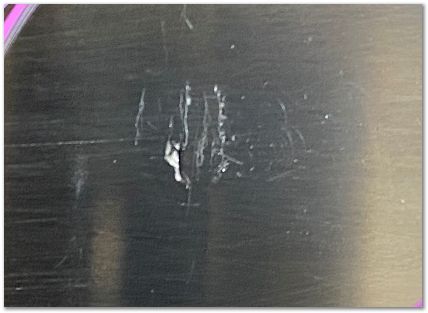 Cluster of cracks, ~6 mm long, 120 mm from the edge of the race. |
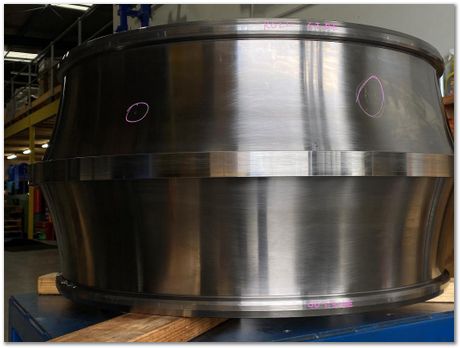 Circle on left is the area where the 6 mm cluster of cracks was observed (area 2), and on the right, the 35 mm crack (area 1). |
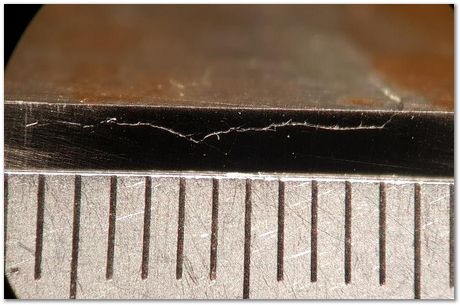 12 mm long (sub-surface crack) on transverse face of sample extracted from inner race. Crack 0.5-1 mm below rolling surface |
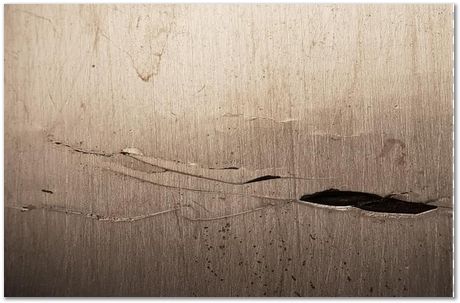 The inner race, 35 mm crack in area 1. |
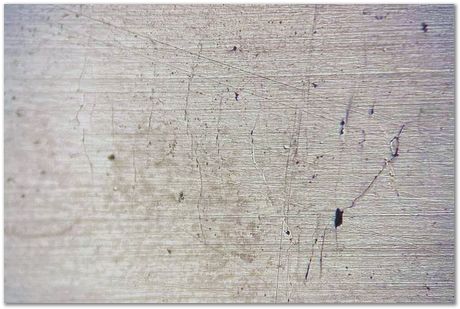 Cluster of fine fatigue cracks in area 1, about 25 mm from the main crack, inner raceway |
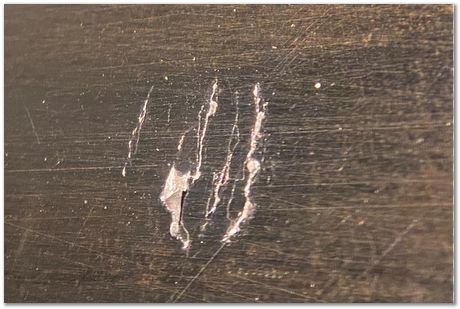 Cracking area 2. Morphology of fatigue cracking consistent with micro-flexing of the bearing inner race. |
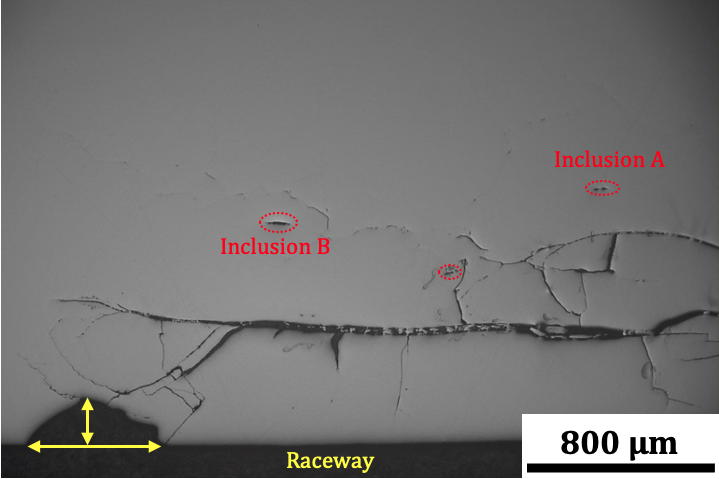 Spall identified by yellow arrows, exposed to inner raceway. Branched subsurface-crack is about 470 µm from rolling surface. Inclusions associated with the cracking, marked. |
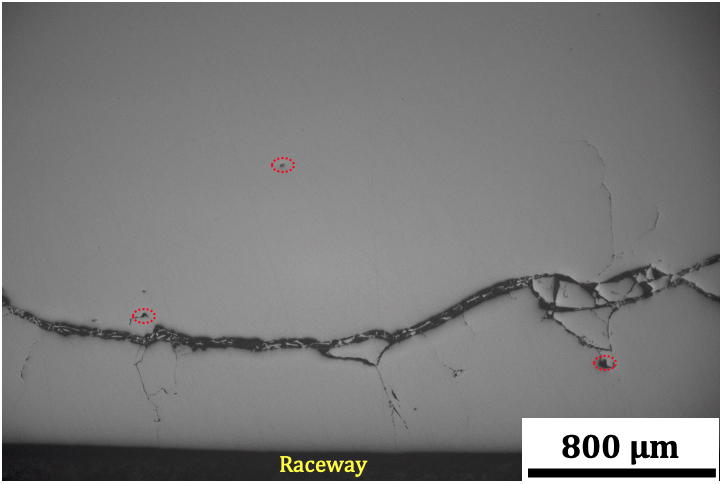 Inner raceway. |
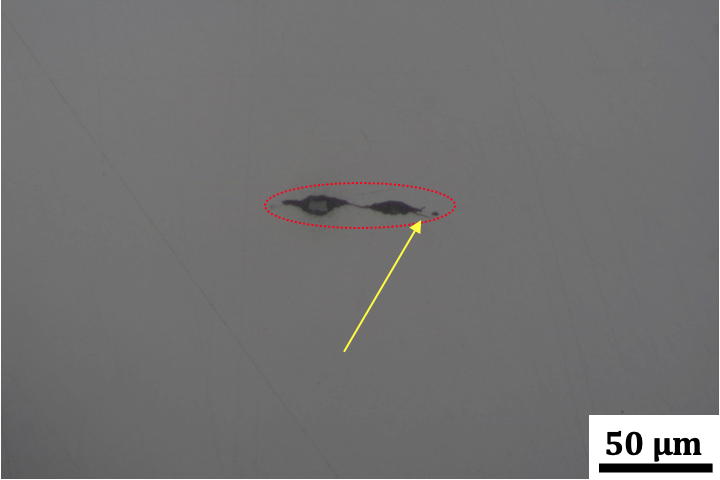 60 µm long, elongated defect. Alloy inclusions identified inside the non-metallic inclusion. Cracks emanate from end of inclusion. |
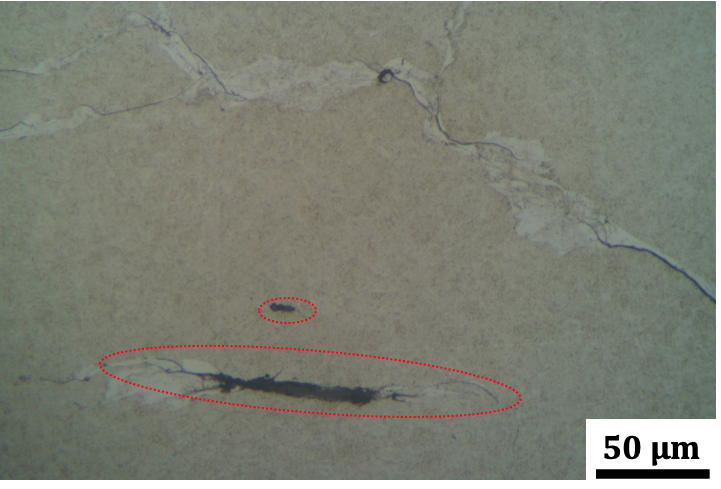 70 µm elongated non-metallic stringer inclusion. Multiple fatigue cracks observed emanating from defect.
|
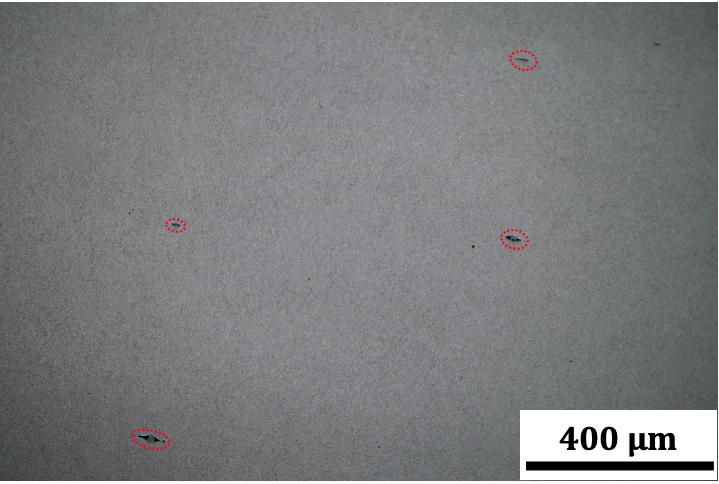 Non-metallic stringer inclusions oriented in the forging direction |
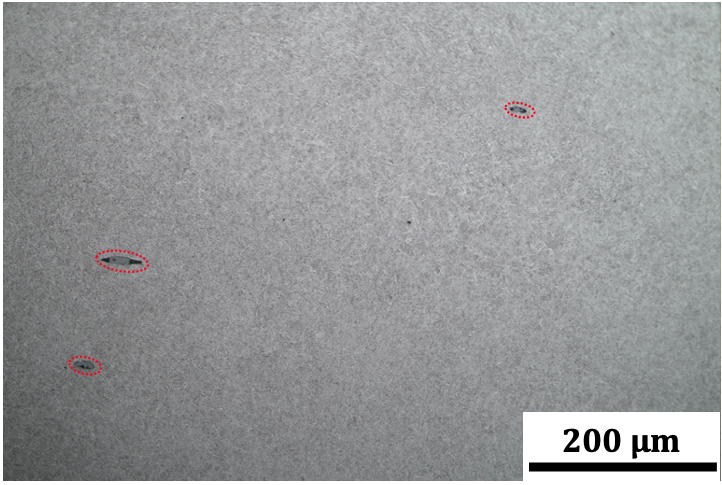 III |
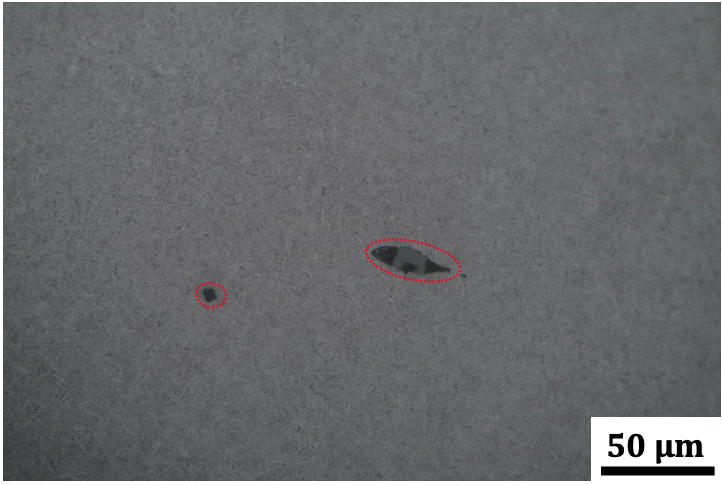 Tapered voids on either side of inclusion, concentrating stress in the vicinity. |
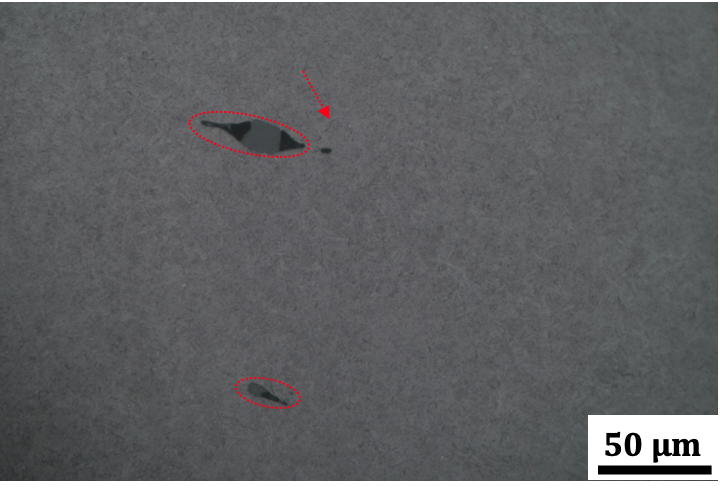 III |
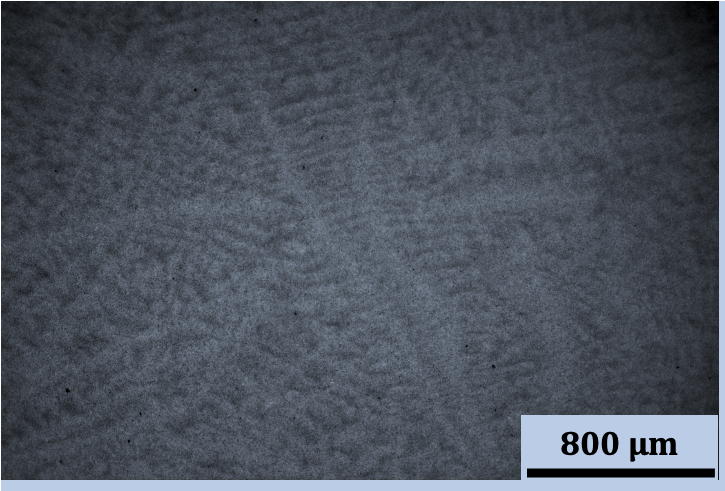 Solidification dendrites consistent with minimal deformation of the as-cast microstructure. |
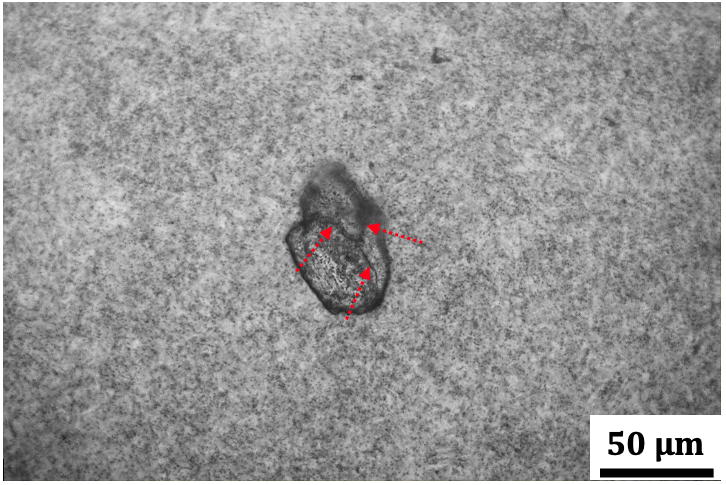 Micro-shrinkage between dendrites - the stain around the shrinkage is due to etchant leaking out during metallographic preparation. |
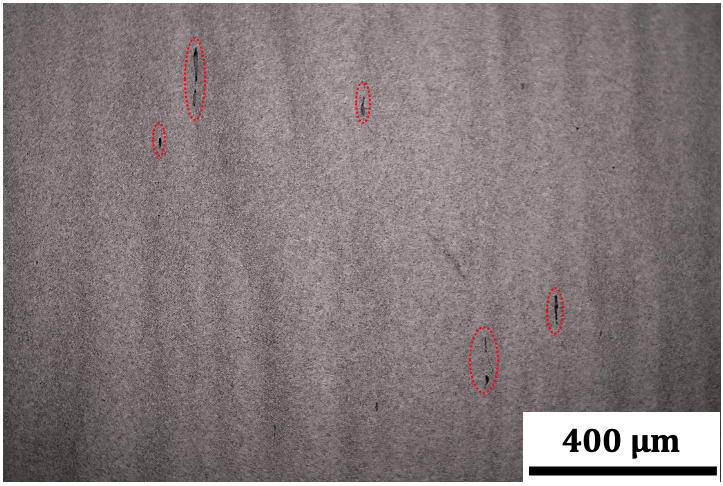 Deformation during manufacture has not managed to seal the interdendritic-shrinkage by compression and welding. |
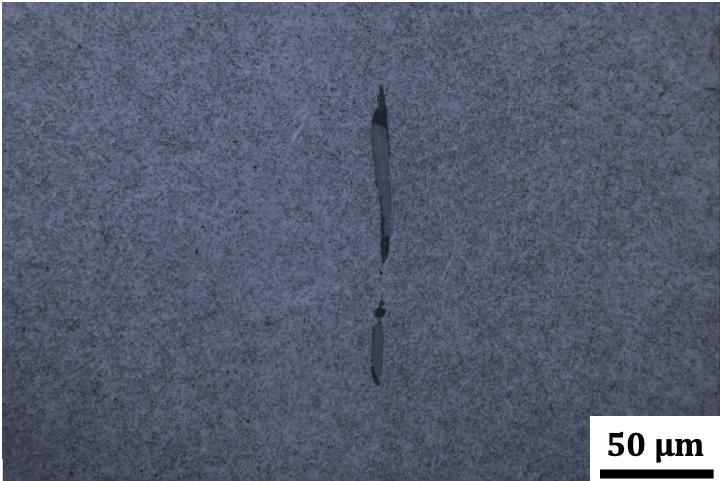 130 µm inclusion elongated along forging direction, with micro-voids at the ends. |
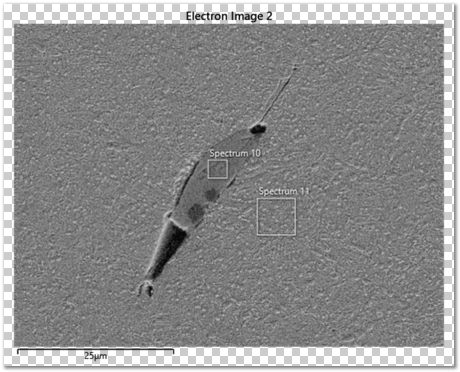 III |
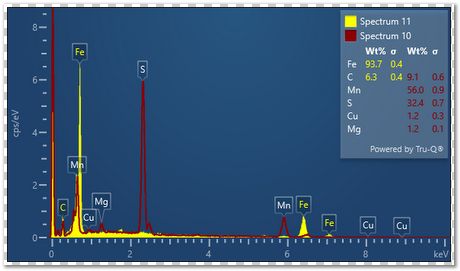 Energy dispersive X-ray analysis of inclusion on the left image. |